
Results of Vchasno.EDI implementation


About Biosphere Corporation
The history of the company began in 1997 with the distribution of goods of international brands Kimberly-Clark, SCA International and TZMO. In 2002, we launched our own production facility, the KPD plant, which allowed us not only to sell but also to manufacture products.
Since 2008, the company has been growing dynamically – new plants have been opened, in particular in Letychiv, and in 2009, we started producing B2B products under the PRO service brand. In 2014, the Polygreen plant was opened in Fastiv (Kyiv region), one of the largest recycling plants in Ukraine.
In 2015, together with Groupe Lemoine, a plant for the production of cotton products was opened in Estonia. In 2020, Go Green biodegradable bags were presented – the first in Ukraine in their segment. In 2021, a logistics complex was built in Dnipro, and in 2022, the company acquired the Alufix brand with production facilities in Romania. Products under this brand are sold in 15 European countries, 70% of which are manufactured in Ukraine.
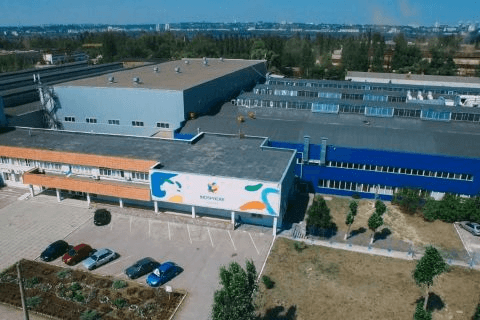
Today, Biosphere has a wide geographical presence and, thanks to its own production and distribution, provides quality products to consumers in different regions.
The company has four main business directions:
✔︎ Household — products for the home, storage and cooking (brands Freken Bock, Vortex, Alufix);
✔︎ Hygiene — personal care products (brands Selpak, Novita, Smile);
✔︎ Biosphere Professional — products for professional use (brands Tork, ProService);
✔︎ Tea&Food — a new direction of food production
Many people know the name Biosphere, but not everyone realizes that they use its products every day.
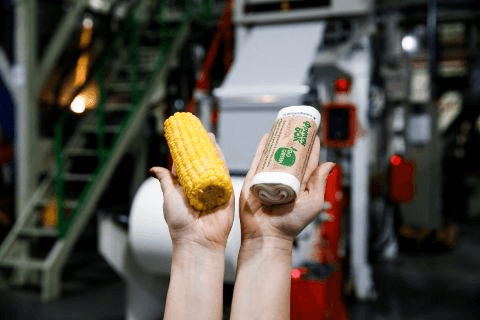
Our challenges and needs: what led Biosphere to implement Vchasno.EDI?
In 2021, we asked Vchasno to optimize the exchange of orders with the Rozetka network. At the time, integration was critical, as working through the web platform was not suitable due to the large volume of documents.
The process was not easy because Rozetka uses many types of documents. We started with the main ones – orders (ORDER), confirmations (ORDRSP), and shipping notifications (DESADV), and later added a digitally signed invoice, a chain of documents for the return of goods, and other important reports.
If at first we worked only with Rozetka, now the electronic document flow covers 23 retail chains. And instead of 50-55 documents in 2021, we are already processing tens of thousands.
The key trigger was a change in tax legislation that extended the document retention period from three to five years. This led to an increase in logistics and storage costs, so we were looking for a solution. The introduction of EDI in our work with distributors was a logical continuation of our development.
How were the processes set up before the implementation of Vchasno.EDI?
Before automation was introduced, some processes were partially automated, such as data exchange and upload. However, some operations were still performed manually. This is how the process looked like:
- Operators created order templates and sent them to distributors via various channels – mail, FTP, etc.
- The distributor filled out the order and returned it.
- Then, the customer service department loaded these orders into the ERP system and processed them.
This process had its drawbacks:
- Dependence on the human factor (absence of an employee, mistakes in filling out, etc.).
- High workload for the logistics service that controlled the document flow.
EDI Implementation Plan
Automating the exchange of EDI documents through the Vchasno.EDI service significantly speeds up data exchange between companies, reduces the amount of manual work, and minimizes the risk of errors.
However, EDI implementation requires careful preparation, as each company has its own specific business processes and integration requirements.
“EDI Implementation Plan”
-
1Analysis and adaptation of the existing process through the EDI platform;
-
2Development of information letters for distributors;
-
3Integration of all necessary functionality into the ERP system;
-
4Dividing the connection process into stages.
About the process of integrating EDI into the ERP system
We have implemented an electronic digital signature module that allows operators to sign documents without having to switch to other systems. This greatly simplifies and speeds up workflows.
We also finalized data exchange with Vchasno.EDI. First, we analyzed the existing processes, optimized the transfer of key primary documents, and gradually integrated all these mechanisms into our digital archive. Now it stores documents from all systems with a certified digital signature, so the accounting department and counterparties can easily and quickly find the files they need.
In addition, we have fully integrated the EDI platform with our archive of legally significant documents (LSD), which provides a single point of access to all electronic documents and their convenient processing
Stages of implementing order exchange
After analyzing the entire process, we identified three main stages of implementation that formed the ROADMAP of integration.
The first stage is connecting the distributor to the existing functionality. Since most partners work with different networks and are integrated with EDI providers, they already know how to create and send orders, confirm them, and send shipment notifications. At this stage, it is only important to synchronize these processes with our requirements.
The second stage we are currently at is finalizing the process of receiving return documents from partners. Since they are the ones who generate and send these documents, we are preparing our ERP system to process them correctly. This means adapting the system to document templates, automating their parsing, and generating relevant internal documents. In addition, we integrate all these mechanisms into the company’s internal business logic, including additional checks, distributions, and controls.
The third stage we are all moving towards is the introduction of eTTN. This will significantly reduce the cost of storing documents, eliminate the need for physical archives, and greatly simplify the search for information, especially for a long period (3-5 years). We value our resources and employees, so we strive to automate all possible processes to minimize routine work and increase efficiency.
Main challenges
Every project in our company is, first and foremost, about speed. We are constantly opening new plants, branches, and facilities.
However, the speed of connecting our partners to the document exchange remains a challenge. Not everyone understands the value of automation, and this process often resembles a chess game: one step – waiting, another step – waiting again.
I am confident that we will achieve the result, but I would like it to happen faster and our partners to be more motivated to change.
Benefits received by the company
We are well aware of the complexities of implementing automation. It’s always a difficult process that requires resources, team adaptation, and changes in the usual business processes.
But we are confident that automation will bring tangible benefits not only to us but also to our partners.
In particular, the introduction of EDI allows:
- Speed up the exchange of documents by at least 2-3 times.
- Significantly reduce the cost of processing them in the logistics and customer service departments.
- Minimize the risk of losing documents and simplify their search.
- Optimize the financial costs of document management.
The main goal is not just to convert documents into electronic format, but to ensure efficient, secure and fast document flow. In a time of war, such solutions are even more important, as data protection and accessibility are critical.
More about the electronic data exchange service Vchasno.EDI
Get acquainted with all the possibilities of the service and start cooperation.